Mastering Root Cause Analysis: A Review of the Best Investigation Tools
Table of Content
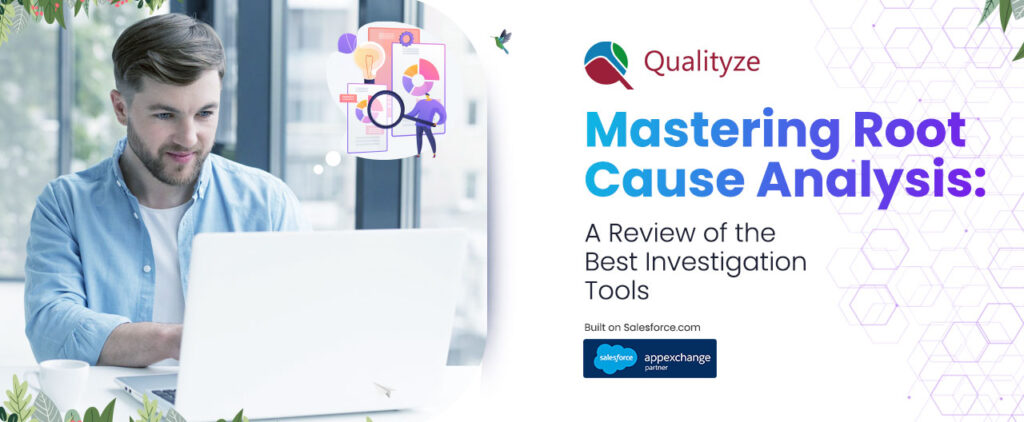
Qualityze Podcast : Mastering Root Cause Analysis: A Review of the Best Investigation Tools
Welcome to the second series of problem or issue investigation processes. In this series, we’ll discuss the several different and best investigation tools that can be used to identify and resolve problems or issues in various settings, including business, manufacturing, and healthcare. Listed below are some of the most commonly used tools and how to use them efficiently
5 Ws
The 5Ws (Who, What, When, Where, Why) tool is a simple yet effective method for gathering information about a particular problem or situation. It can be used to identify the key facts and details necessary to understand a problem or make a decision. Here are the steps for using the 5 Ws tool:
- Define the problem or situation: Clearly define the issue you want to address.
- Ask “who “: Identify the people or organizations involved in the problem or situation. This includes both those affected by the problem and those who may be able to help solve it.
- Ask “what”: Identify what has happened or what is currently happening that is causing the problem or situation.
- Ask “when”: Identify when the problem or situation occurred or when it is expected to occur.
- Ask “where”: Identify where the problem or situation is occurring or originated.
- Ask “why”: Identify why the problem or situation occurred, including the underlying causes or contributing factors.
- Using the 5 Ws tool, you can gather the key information needed to understand a problem or situation and develop an effective action plan.
5 Whys
It’s important to focus on the problem, ask open-ended questions, involve multiple perspectives, and persist in getting to the root cause. The 5 Whys tool is typically used to identify the root cause of a problem. It is a simple, but powerful tool that involves asking “why” five times to get to the underlying cause of an issue. The 5 Whys tool is particularly useful when dealing with complex or recurring problems and when you want to get to root causes rather than addressing the symptoms.
To use the 5 Whys tool:
- Start by identifying the problem or issue you want to investigate.
- Ask “why” the problem occurred and write down the answer.
- Use that answer to ask the next “why” question and continue this process until you have asked “why” five times or until you have found the root cause.
For example, if the problem is that a machine is not working properly, you might ask:
- Why is the machine not working? (e.g., because it won’t start)
- Why won’t the machine start? (e.g., because the power source is not working)
- Why is the power source not working? (e.g., because the circuit breaker tripped)
- Why did the circuit breaker trip? (e.g., because the machine was overloaded)
- Why was the machine overloaded? (e.g., because the operator did not follow the instructions)
- By asking “why” five times, you can identify the root cause to prevent it from happening again.
Nonconformance Management Software optimizes your quality program to streamline ISO 9001 compliance. Qualityze makes the top choice by reducing rework, eliminating product recalls and improving customer satisfaction.
Fishbone Diagram
A fishbone diagram, also known as an Ishikawa diagram or a cause-and-effect diagram, is typically used in problem-solving and root-cause analysis to identify the potential causes of a problem. It is a graphical representation that displays all the possible causes of a problem and their relationships.
The fishbone diagram is particularly useful when dealing with complex problems where multiple causes may contribute to the issue. It is also helpful in bringing together different perspectives from individuals or teams involved in the problem and identifying the most significant causes to prioritize efforts for resolution. Fishbone diagrams are commonly used in quality control, product development, process improvement, customer complaints, risk management, and other applications. To use the fishbone tool, follow these steps:
- Clearly define the problem or effect that you want to analyze.
- Draw a large “head” at the end of a horizontal line, representing the problem or effect.
- Draw several “bones” branching off the main line, representing the different categories of potential causes. Common categories include materials, methods, people, equipment, environment, and management.
- Identify specific causes within each category and write them on the corresponding bones.
- Analyze the causes and look for patterns or connections between them.
- Use the information gathered to plan to address the problem or effect.
- Implement the plan and evaluate its effectiveness in resolving the issue.
To use the Fishbone diagram tool effectively, involving a cross-functional team with a range of knowledge and expertise related to the problem is important. The team can brainstorm potential causes and then organize them into categories that align with the various “bones” of the fish. This can help to identify the most likely root causes and to develop solutions to address them. Quality management software for manufacturing of Qualityze is designed with cloud-based QMS system that allows to optimize and automates all the aspect of global manufacturing management process to truly leverage manufacturing capability to be a competitive force.
Pareto Chart
The Pareto chart is a graphical tool used to identify the key contributors to a problem. For example, it states that roughly 80% of effects come from 20% of causes. The Pareto chart is particularly useful for identifying the most significant factors contributing to a problem, allowing you to focus on areas where you can make the biggest difference.
Here are some steps for using the Pareto chart:
- Define the problem or issue: Identify what problem or issue you want to investigate using the Pareto chart.
- Collect data: Collect data on the problem or issue. This can be done using surveys, customer complaints, or any other appropriate data collection method.
- Determine the categories: Determine the categories of the data you collected. For example, if you are investigating customer complaints, you might categorize them by the type of complaint (e.g., delivery time, product quality, customer service).
- Calculate the frequency or percentage: Calculate the frequency or percentage of each category. To do this, count how many times each category appears in the data.
- Create the chart: Create the Pareto chart by plotting the categories in descending order of frequency or percentage. This can be done using a bar chart, with the tallest bar representing the category with the highest frequency or percentage.
- Analyze the chart: Analyze the chart to determine the most significant factors contributing to the problem or issue. Focus on the categories at the top of the chart, representing the areas where the most improvement can be made.
The Pareto chart can be used in various applications, including quality control, process improvement, and customer service.
Related Article: Root Cause Analysis: Different Techniques with One Goal
Failure mode and effects analysis (FMEA)
FMEA tool is typically used during the design or manufacturing process to identify potential failures and their impact on the product or process. FMEA is a proactive tool used to assess the risks associated with potential failures and to implement appropriate measures to reduce or eliminate those risks.
The steps for conducting an FMEA include the following:
- Define the scope and objective of the analysis
- Create a team to conduct the analysis
- Identify the components or processes to be analyzed
- List all the potential failure modes for each component or process
- Identify the potential effects of each failure mode
- Assign a severity rating to each effect
- Identify the potential causes of each failure mode
- Assign a likelihood rating to each cause
- Determine the current controls in place to detect or prevent each failure mode
- Assign a detection rating to each control
- Calculate the risk priority number (RPN) for each failure mode by multiplying the severity, likelihood, and detection ratings
- Prioritize the failure modes based on their RPNs
- Develop and implement appropriate actions to reduce or eliminate the risks associated with the highest-priority failure modes
Establishing an interval to review and update the FMEA periodically is always a good practice to ensure continued effectiveness. Quality management software for lifescience is one of the most advanced solutions for quality management in highly regulated fields. The process of configurable and easy-to-use features ensures a smooth transition process.
Thought Map
A thought map, or mind map, or concept map is a diagram used to visually organize information around a central idea or concept. It can be useful for problem investigation as it allows you to break down a complex problem into its parts and visualize the relationships between them.
To use a thought map for problem investigation, start by writing the problem statement in the center of the map. Then, brainstorm all possible causes or contributing factors to the problem and write them down as branches stemming from the center. Next, you can further brainstorm sub-causes or related factors from each branch, creating a branching hierarchy of ideas.
Use colors, symbols, and images to help organize and categorize the information, making identifying patterns and relationships between the different factors easier. By creating a thought map, you can gain a clearer picture of the problem and its underlying causes, making it easier to develop a targeted solution.
Related Article - Simplified Problem Solving: Automated RCA for Recurring Safety Issues
Timeline of Changes
A timeline of change is a graphical representation of changes that have occurred over time. It is a useful tool for problem investigation when the problem is related to changes that have taken place. Here are the steps for using a timeline of change:
- Identify the problem and the time frame: Clearly define the problem and identify the time frame over which the problem has occurred.
- Gather information: Collect information about the changes that have occurred during the time frame. This information could include any changes to processes, personnel, technology, or equipment.
- Plot the timeline: Create a timeline that covers the time frame and plot the changes that have occurred during that time. You can use a horizontal line to represent the timeline and vertical lines to indicate the change points.
- Analyze the timeline: Analyze the timeline to identify any patterns or trends in the changes that have taken place. Look for any correlations between the changes and the problem.
- Determine the root cause: Use the information gathered from the timeline to determine the root cause of the problem. You can use other problem-solving tools, such as the Fishbone diagram or Root Cause Analysis, to help you with this step.
Once the root cause has been determined, implement a solution to address the problem. Finally, monitor the situation to ensure that the problem has been resolved.
The entire process can be made easier using a comprehensive and efficient CAPA management software solution like Qualityze. The user-friendly interface and powerful features enable you to streamline your CAPA processes, identify and address issues, and ensure compliance with regulatory requirements.
One of the biggest advantages of using Qualityze is its ability to integrate with various and best investigation tools without any hassles or groundwork. This means you can choose the tool that works best for your organization, whether it’s a root cause analysis tool, fishbone diagram, or 5 Whys analysis, and seamlessly incorporate it into your CAPA process.
By using Qualityze, you can significantly reduce the time and effort required for CAPA management while also improving the quality and effectiveness of your best investigation tools.
For additional information, kindly contact us via email at info@qualityze.com or call us at 1-877-207-8616. Our team of customer success representatives is readily available to provide you with any assistance.
Share
The Start of Something Amazing.
Request Demo
Products
Industries
Company